Brake Judder – Preventative Steps
29 Sep 2021
Our articles Understanding brake judder and Bedding in & Material Transfer Process should have provided you with a better understanding of braking technology. Armed with that information, here is a helpful article on preventative steps that can be taken to prevent brake judder.
Pre-Inspection
- Test drive the vehicle prior to removal of any parts to confirm any symptoms.
- Visually inspect the tyres. Uneven tyre wear, radial separation and damage to the tyre are causes of symptoms that can sometimes be mistaken for brake related issues.
- Check the condition of the wheel bearings. A worn bearing can also cause excessive lateral runout, which may cause the brakes to pulsate or pull.
- Examine the steering and suspension bushes and joints for any free play. Worn steering and suspension bushes will not be able to absorb vertical and lateral forces produced by the vehicle when braking and can cause juddering.
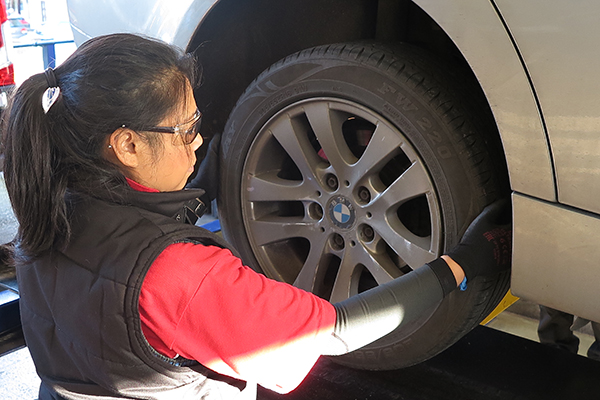
Removal
- Check that the pads can move freely in the caliper carrier, corrosion build up can cause the pads to seize. *
Inspect the caliper fingers and piston contact points, excessive corrosion can cause misalignment of the pads. *
Completely remove the caliper to enable inspection of both caliper sliders. Deteriorated sliders and rubber boots can prevent free movement. If in doubt of their condition, please renew. *
Manually retract the caliper pistons to check for free movement. *
Measure the brake discs, using a micrometre, in at least 8 different equidistant points around its perimeter, 2.5mm from the outer edge. A brake disc with that exceeds the manufacturer’s tolerances (see note overleaf) of thickness variation will result in brake torque variation resulting in brake judder.
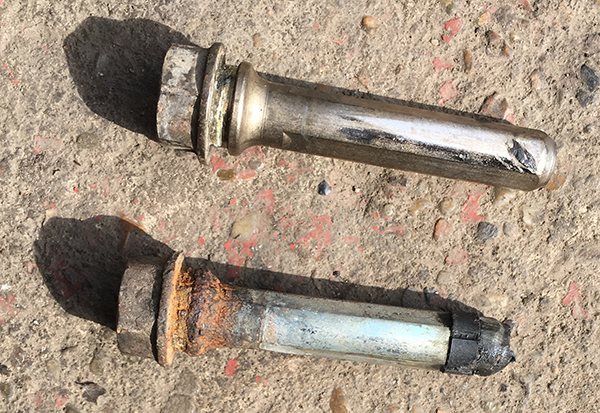
* Anything interrupting free movement of brake components will interrupt the even material transfer process, leading to excessive DTV eventually resulting in brake judder.
Preparation
- Remove corrosion from the caliper carrier, caliper fingers and piston contact points using a tool that will not compromise the metal. **
- Inspect the hub and thoroughly clean the corrosion build up to bare metal using a tool that will not compromise the metal. **
- Treat and protect all the above surfaces, by applying a wash proof, metal free lubricant with a high melting point to prevent galvanic corrosion. **
- Completely remove all sliders to enable through cleaning of the sliders and their cavities.
- Treat and protect the sliders, by applying rubber compatible lubricant that repels moisture to ensure free sider movement.
** Corrosion build up alters the tolerances of braking components, please see our article Corrosion and how it affects braking systems for a detailed explanation.
Refitting
- Brake discs must always be replaced as an axle set to ensure consistency in braking.
- Clean the disc and mounting surface to ensure that it is clean. A foreign object, trapped between the mounting surface of the disc and the hub will cause excessive lateral runout, leading to excessive DTV and eventually brake judder.
- If equipped with a disc locating screw renew and replace. The screw secures the brake disc and prevents contamination entering behind the brake disc.
- Mount & secure the disc and check for disc run out using a DTI gauge, this should be no more than the vehicle manufacturer’s tolerances. If the manufactures’ data is unavailable, please refer to the following guide.
The precise threshold varies from model to model, dependent upon the general compliance built into the vehicle’s braking, suspension and steering systems. Anything more than this will cause excessive lateral runout of the brake disc, leading to DTV and eventually judder.
- Examine and thoroughly clean the contact surface of the wheel before refitting. Contamination or poorly refurbished allow wheels will cause excessive lateral runout leading to brake judder.
- Torque wheel bolts to the correct torque following the correct torqueing sequence. Incorrect torque on the wheel bolts could damage the disc hat and distort the hub contact surface, causing excessive lateral runout leading to brake judder.
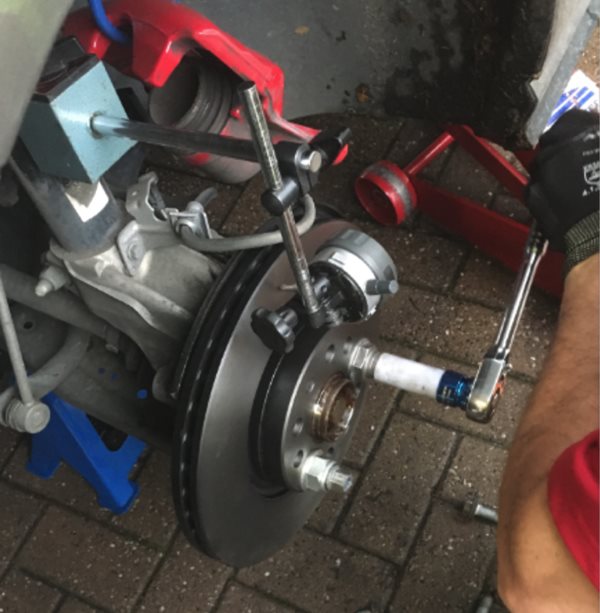
Aftercare
- Follow the recommended bedding in procedure that is detailed in the Bedding in and Material Transer Process article.
- The process will take longer for fully coated discs as the coating will need to be completely removed for the material transfer process to occur evenly onto the disc surface.
- Make the driver aware of the recommended “after care” for about 200 miles to ensure even material transfer.
- Even after 200 miles incorrect braking technique will affect the even material transfer process. Repeated heavy braking after high speeds, depressing the brake for long periods of time while stationary (when brakes are hot), continuous braking on steep declines instead of engine braking and feathering the brake pedal can disrupt the even material transfer process and cause DTV leading to brake judder.
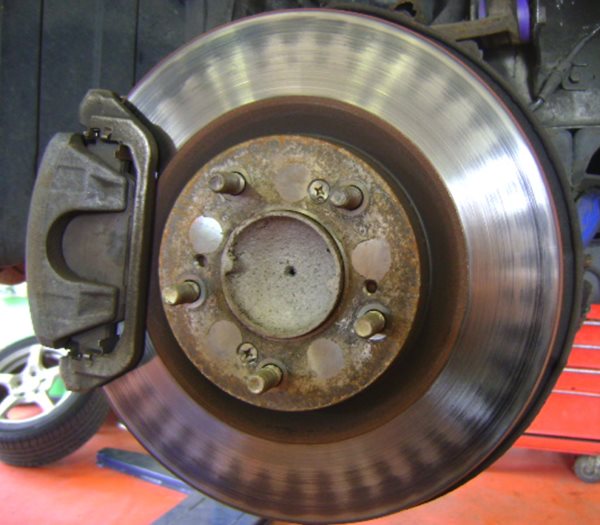
Apec Braking start the aftercare process by having an additional High Pressure Treatment process as part of manufacture of our brakes, to provide superior initial performance and easier bedding in. Apec brake discs are only coated on the hub and edge surface. But when it comes to the fricton surface, we stop – so there’s no coating to contaminate the pads and reduce their efficiency.
TECHMATE is here to make your life easier
When you need to know more about braking with Apec, ask TECHMATE.